Machine parameters for spindles, 3 mac h ine p a ra met e rs (mp) – HEIDENHAIN CNC Pilot 4290 V7.1 User Manual
Page 573
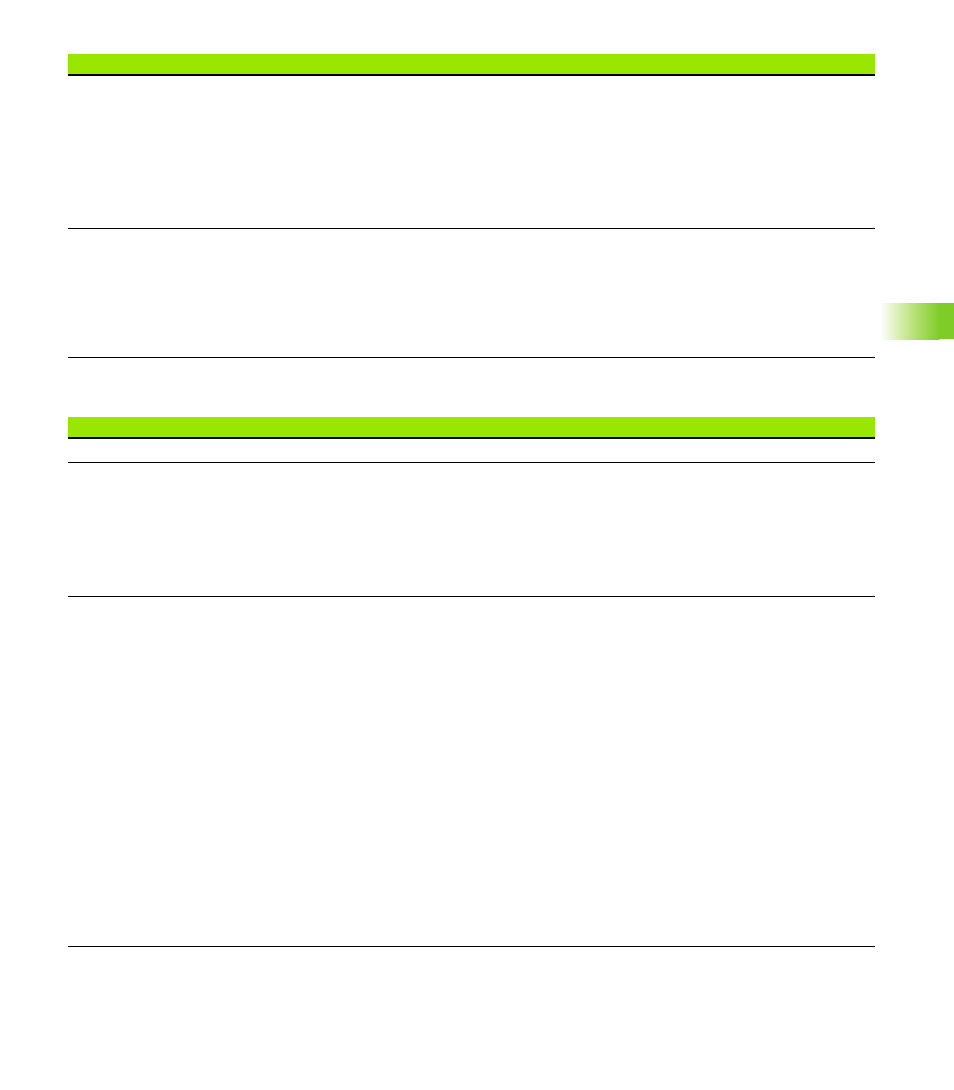
HEIDENHAIN CNC PILOT 4290
573
7.
3 Mac
h
ine P
a
ra
met
e
rs (MP)
Machine parameters for spindles
211, 261, ..
Position of the touch probe or optical gauge
To define the position of the probe, enter its external coordinates (reference: machine zero point). To define the
position of the optical measuring system, enter the position of the cross hairs (+X/+Z).
Position of touch probe/optical gauge in +X
Position of touch probe in –X
Position of touch probe/optical gauge in +Z
Position of touch probe in –Z
511..542,
561..592, ..
Description of tool holders
These parameters describe the positions of the tool holders relative to the tool-carrier reference point.
Distance to carrier reference point X/Z/Y: Distance between reference point of tool carrier and reference
point of tool holder.
Compensation X/Z/Y: Compensation value for the distance between reference point of tool carrier and
reference point of tool holder.
Slide parameters
Spindle parameters
804, 854, ..
Spindle protection zone monitoring is not used at present.
805, 855, ..
General spindle parameters
Zero point shift (M19): Defines the distance between the reference point of the spindle and the reference
point of the encoder. After receiving the reference pulse from the encoder, the value determined is
transferred.
Number of revolutions for backing off: Number of spindle revolutions after the spindle has stopped in
Automatic mode. (When using low spindle speeds, additional spindle revolutions are necessary to relieve the
tool.)
806, 856, ..
Tolerance values of spindle
Speed tolerance [%]: The system proceeds from a G0 block to a G1 block as soon as the status “Speed
reached” is attained. When the speed lies within the tolerance range, the status is attained. The tolerance
value refers to the nominal value.
Position window, position [°]: After the spindle has stopped at a defined position (M19), the system
proceeds to the next block as soon as the status “Position reached” is attained. When the difference
between nominal and actual value lies within the tolerance range, the status is attained. The tolerance value
refers to the nominal value.
Speed tolerance, synchronization [rpm]::Criterion for status “Synchronization reached.”
Position tolerance, synchronization [°]: Criterion for status “Synchronization reached.”
Notes on synchronization parameters:
The synchronization parameters depend on the settings of the slave spindle.
The “Synchronization reached” status is attained when the actual speed difference and the actual position
difference between the spindles to be synchronized lies within the tolerance range. When the status
“Synchronization reached” is attained, the torque of the guided spindle is limited.
The tolerances which are actually attainable on the machine must not be undercut when setting these
parameters. The value programmed here must be set to a value greater than the sum of the maximum
differences in the speeds of the guiding and guided spindles (approx. 5 to 10 rpm).