3 mac h ine p a ra met e rs (mp) – HEIDENHAIN CNC Pilot 4290 V7.1 User Manual
Page 576
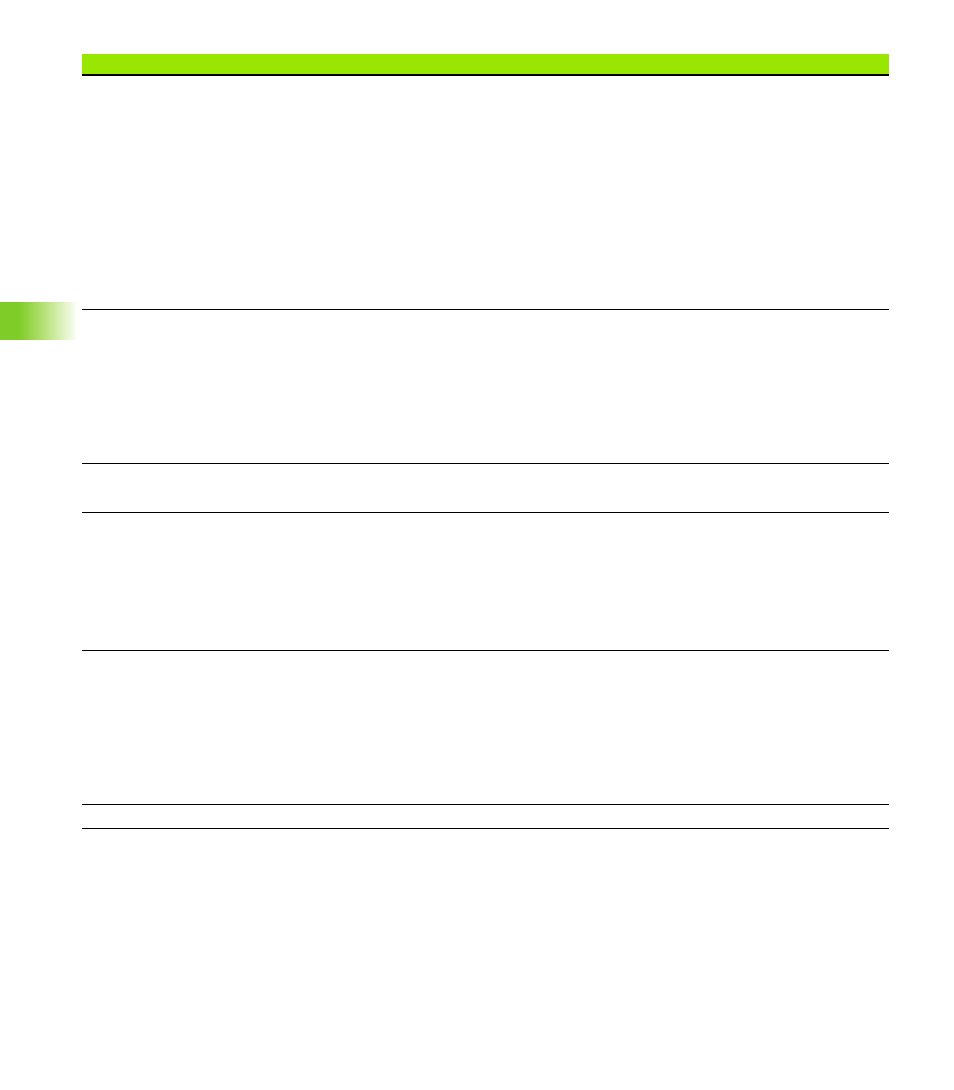
576
7.
3 Mac
h
ine P
a
ra
met
e
rs (MP)
1110, 1160, ..
Load monitoring for linear axis
Evaluation: Load monitoring
Start-up time for monitoring [0..1000 ms]: The load monitoring function is not activated if the nominal
acceleration of the spindle exceeds the limit value (limit value = 15% of acceleration ramp / brake ramp).
As soon as nominal acceleration falls below the limit value, the monitoring function is activated after the
start-up time for monitoring has elapsed.
Evaluated if “Omit paths of rapid traverse” is active.
Number of measured values to be averaged [1..50]: The mean value is calculated from the number of
values to be averaged. This reduces the sensitivity to short-term peak load during monitoring.
Maximum torque is not used at present.
Reaction delay time P1, P2 [0..1000 ms]: The system reports a limit violation as soon as the delay time
for P1 or P2 (limit torque 1 or 2) has been exceeded.
1112, 1162, ..
Traversing to a fixed stop (G916) in linear axis
Evaluation: G916 Traverse to fixed stop
These parameters apply to the linear axis for which G916 has been programmed.
Lag error limit: The slide is stopped as soon as the following error (lag error; deviation of the actual from
the nominal position) reaches the following error limit.
Reversal distance: After reaching the “fixed stop,” the slide is moved back by the reversal distance (to
reduce the stress).
1114, 1164, ..
Zero point offset during conversion in linear axis
NC zero offset: Length by which the machine zero point is shifted during conversion (G30).
1115, 1165, ..
Parting control (G917) for linear axis
These parameters apply to the linear axis for which G917 has been programmed.
Evaluation: G917 Controlled parting using following error (lag error) monitoring
Lag error limit: The slide is stopped as soon as the difference between actual and nominal position has
reached the following error limit. The CNC PILOT reports that it has detected following error.
Feed rate when moving the linear axis using following error monitoring.
1116, 1166, ..
Limit switches, protection zone, feed rates in linear axis
Negative dimension of protection zone
Positive dimension for protection zone: Dimensions for protection zone monitoring (reference:
machine zero point)
Rapid-traverse speed in Automatic mode
Reference dimension: Distance between reference point and machine zero point
1120, 1170, ..
Misalignment compensation for linear axis: Parameters are entered by the machine tool builder.
Parameters for linear axes