Yaskawa MP940 Reference Manual User Manual
Page 264
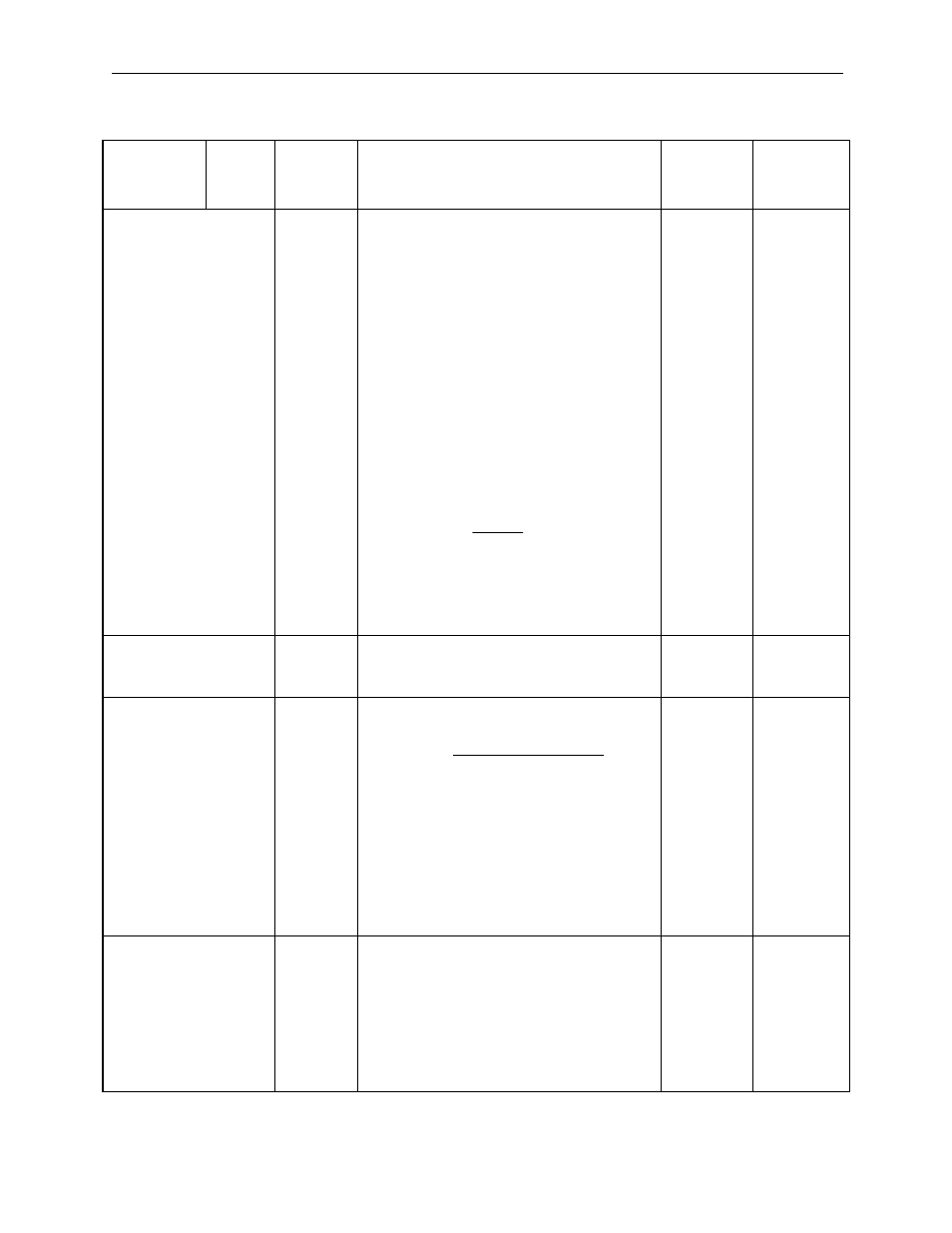
SGDH User Parameters
MotionSuite™ MP940 Machine Controller Reference Manual
6-64
Pn101
Speed Loop Integral
Time Constant
0.01ms
15 ~
51200
Integral elements are kept in the speed
loop so that response can be obtained
even for minute inputs. These integral ele-
ments are delaying elements from the
viewpoint of the servo system. For this
reason, an increase in the time constant
results in lengthened settling time for posi-
tioning, and degradation of responsive-
ness.
Failure to increase the integral time con-
stant to some degree results in a machine
prone to vibration if the load inertia is too
large, or if vibratory elements are included
in the machine system. Use the following
scales.
Ti: Integral Time Constant [s]
Kv: Speed Loop Gain (value calculated in 1)
[Hz]
2000
Speed
Torque
Position
Pn102
Position Loop Gain
1/s
1 ~ 2000
This parameter is not used. (Do not set.)
Set the position loop gain in the SVA set-
ting parameter OWC010.
40
Position
Pn103
Inertia Ratio
%
0 ~ 10000
The factory setting is Motor Axis Conver-
sion Load Inertia = Servo Motor Load Iner-
tia. Obtain the inertia ratio by the above
formula, and set the user parameter
Pn103.
This user parameter is set automatically in
the autotuning operation.
0
Speed
Torque
Position
Pn104
2nd Speed LoopGain
Hz
1 ~ 2000
It is possible to switch between the speed
loop gain, speed loop integral time con-
stant, and position loop gain using Pn100
~ Pn102, and Pn104 ~ Pn106, by the G-
SEL (gain switching (OBC0012)) com-
mand of the MP940 setting parameters.
OBC0012 = 0: Use Pn100 ~ Pn102
= 1: Use Pn104 ~ Pn106
40
Speed
Torque
Position
Gain Related Parameters (Continued)
User
Parameter
Number
Digital
Position
Name
(setting
range)
Content
Default
Setting
Control
Mode
Kv
2
1
2.3
Ti
×
×
≥
π
Inertia Ratio =
Load inertia of motor axis
conversion (JL)
Servo motor rotor inertia (JM)
x 100%